DECARBONISING THE HEAVY TRANSPORT INDUSTRY WITH HYDROGEN
HWR is leading the transport industry on the sustainability journey, driving towards a carbon neutral future.
To reach a carbon neutral future by 2050, big change is needed.
HWR is a big business with big ideas that can action big change. We are New Zealand’s largest transport company. We’ve been in the business for a long time, so we know what works and what doesn’t.
That’s why we’ve invested in dual-fuel hydrogen technology. We believe it’s the way forward for heavy transport.

Dual Fuel Conversion
CH2NGE Fuel Technologies is the future of transportation. With the successful introduction of New Zealand's first dual-fuel milk collection tanker, you can transition your fleet to dual-fuel technology without the risk of stranded assets. Fuel sources are always available, and your payloads remain unaffected. Change is around the corner, learn more here.
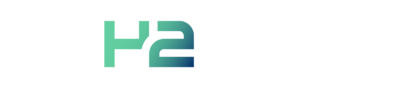
The Plan
For HWR, there are two streams of work in our hydrogen plan: dual fuel technology in truck fleets, and a hydrogen refuelling network. To date we’ve committed over $15 million exploring New Zealand owned and produced hydrogen and trialling dual-fuel technology, addressing both supply and demand.
Dual Fuel
Hydrogen is a future fuel that will transform the transport industry, shifting it from being one of the largest emitters, to one of sustainability's biggest champions.
The key to a successful transition to future fuels is a sustainable and attainable approach.
A dual-fuel approach will allow the entire heavy transport industry to transition to hydrogen as an alternative fuel in a way that is accessible, fair and equitable.
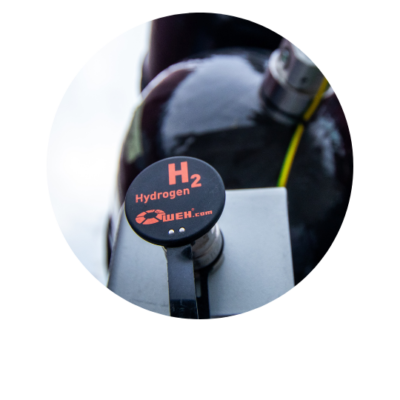
Refuelling Network Development
In order for the heavy transport industry to readily access hydrogen, there needs to be a refuelling network. One of HWR’s companies, Allied Petroleum, has an existing network of fuel stops from the Karikari Peninsula to Stewart Island.
HWR will use the Allied Petroleum network to distribute hydrogen as an alternative fuel by adding the refuelling capability to existing and new sites. Electrolysers will be added across the Allied Petroleum network where their locations would make the most sense. Storage tanks, compressors and dispensers will be added to make sites dual purpose: production and dispensing of hydrogen, alongside diesel and petrol products. For customers, refuelling will look much the same as now, with fuels such as petrol and diesel.
We're working closely with Christchurch’s based engineering innovator Fabrum, a world leader in zero-emission transition, for our end-to-end scalable hydrogen refuelling solution that produces hydrogen on-site.
The first green hydrogen production system is being developed for Southland and will be capable of producing 450kg per day.
Upgrading and transitioning our fleet is only part of the solution. Our plan answers both the supply and demand challenge. Having hydrogen available and accessible for other companies to access across NZ will support other companies to reach their own sustainability goals.
"Hydrogen as an alternative fuel is not just for our fleet... but to help the heavy transport industry as a whole."
- Anthony Jones
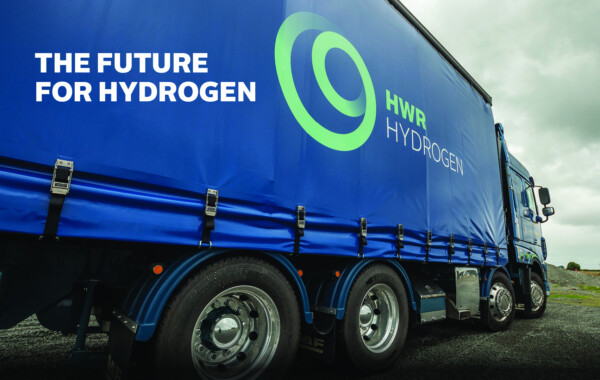
Our partners
We’re proud to partner with the following game-changing companies as we work towards a carbon-neutral future.
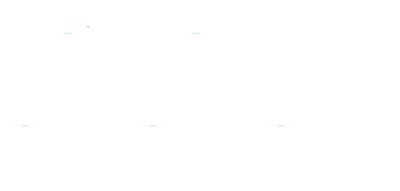
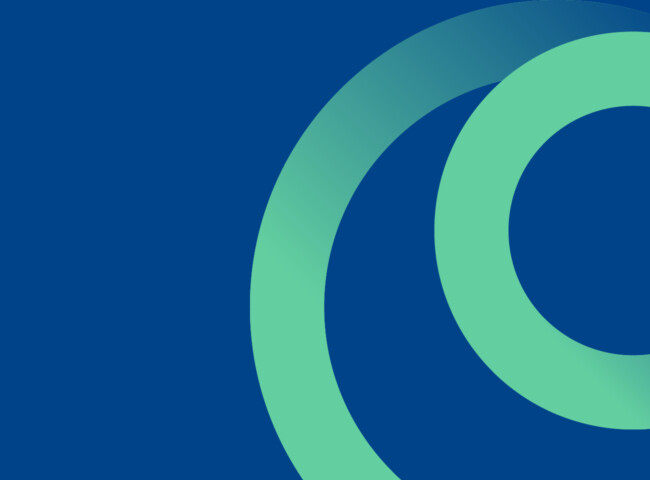